Over 30 Years Production Experience
Provide You with Starch Mogul Production Line Solutions
Trustworthy China Candy Machine Manufacturer
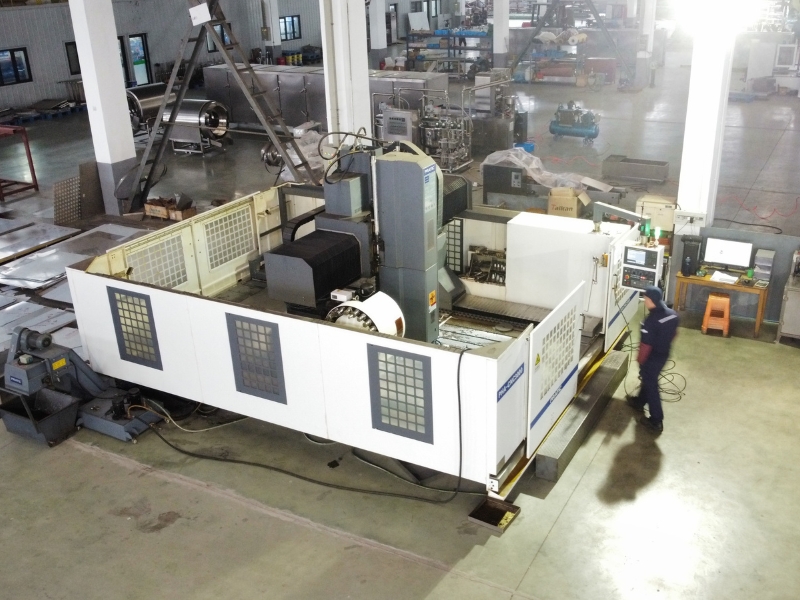
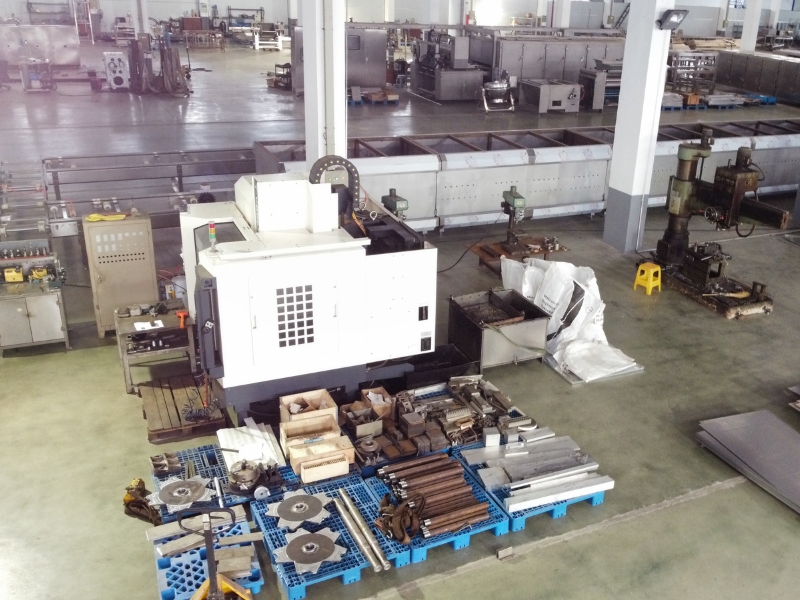
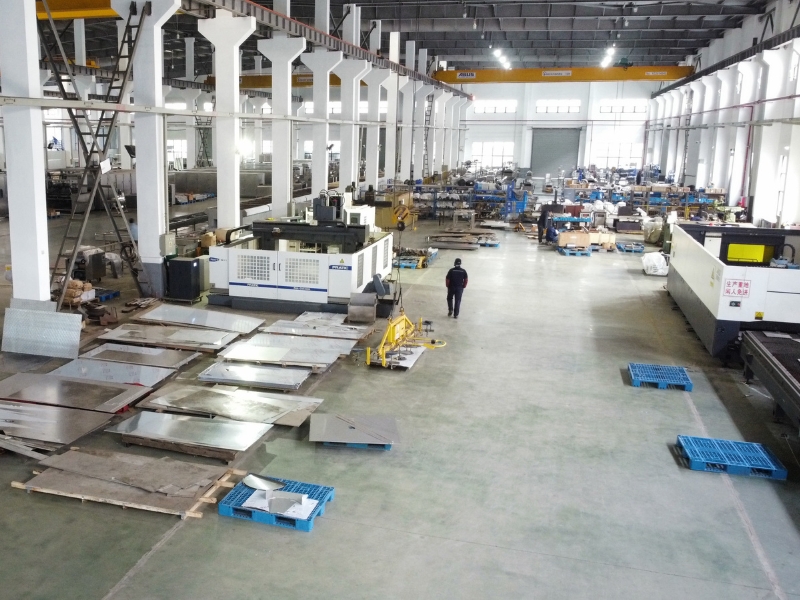
Fully Automatic Model Starch Mogul Line Series

Full Automatic Starch Mogul Line
Junyu-S462
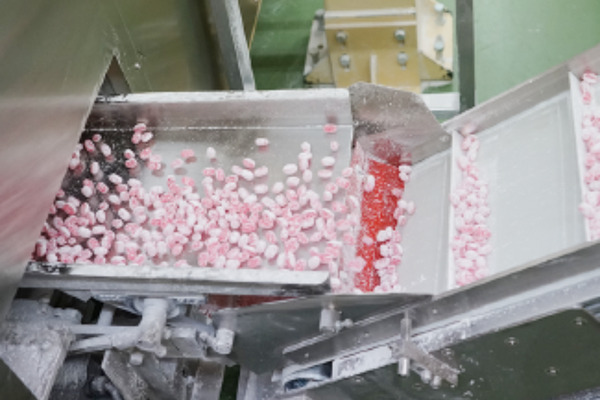
Full Automatic Starch Mogul Line
Junyu-S660
Semi-Automatic Model Starch Mogul Line Series
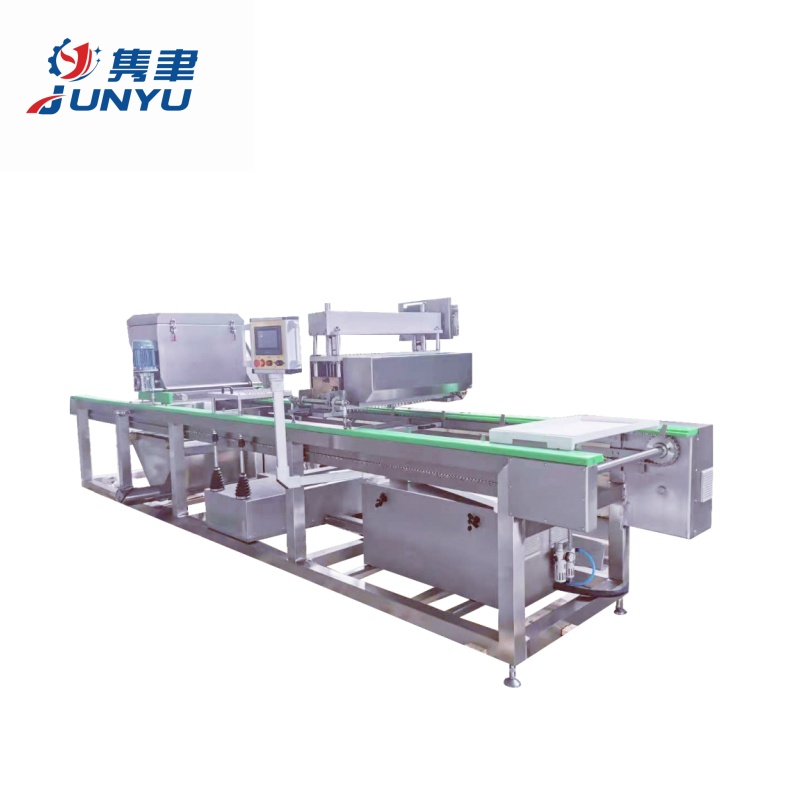
Semi-Automatic Starch Mogul Line Series
Models: JYS-40, JYS-60, JYS-80
Key Specifications:
Related Products

Candy / Gummy Kitchen CIP Cleaning System
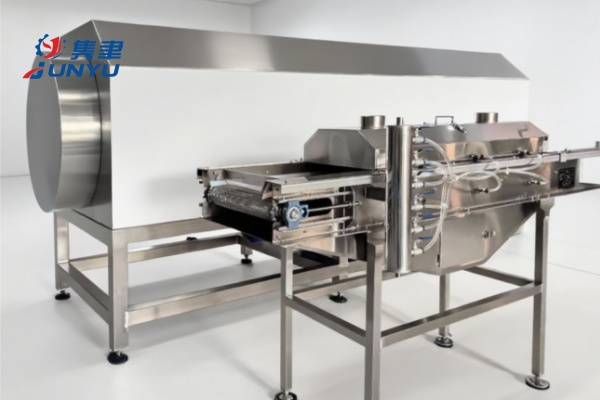
Steam-Humidifying & Sugar-Sanding Machine
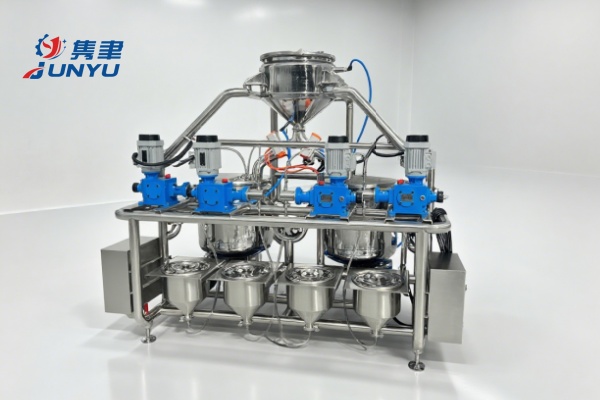
Automatic Weighing & CFA Adding Station
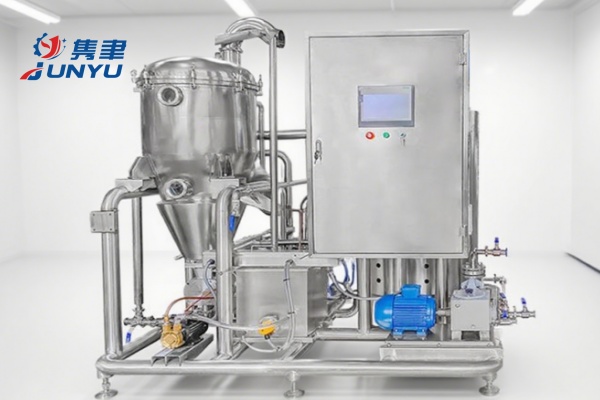
Raising Film Continuous Cooker
Starch Mogul Production Process
1. Kitchen System
Water, glucose syrup, pectin solution and granulated sugar, according to the preset formula of production requirements, complete the automatic premixing of ingredients through a three-point weighing and mixing tank, and the premixed materials are discharged into the dissolving tank (in order to increase the production capacity, two dissolving tanks are equipped , Work alternately), through steam heating, the material is dissolved in the dissolver, the temperature is automatically controlled, the material in the dissolving tank is heated and dissolved to the preset temperature, the steam heating valve is automatically closed, and the stirring is continued for a certain time or temperature, and then added to the gelatin tank According to a batch of gelatin solution, after stirring for a certain period of time, the sugar solution and the gelatin solution are evenly mixed, and then sent to the storage tank through the rotor pump.
The kitchen system consists the raw material preparation system, automatic weighing and dissolving system as recipes, cooking system, CFA system, Aeration system, hot water and warm water system, and so on. With one control group accordingly. Advantages of depositing:
- More Accurate
- Much Faster
- More Clean
- Saving labor
- Recipes in System memory
- Automatically and Continuously
- Stable gummy quality
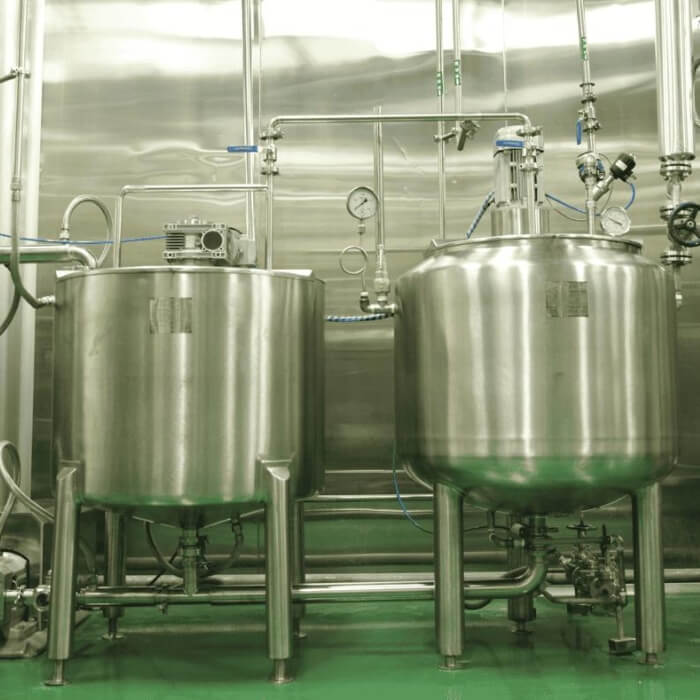
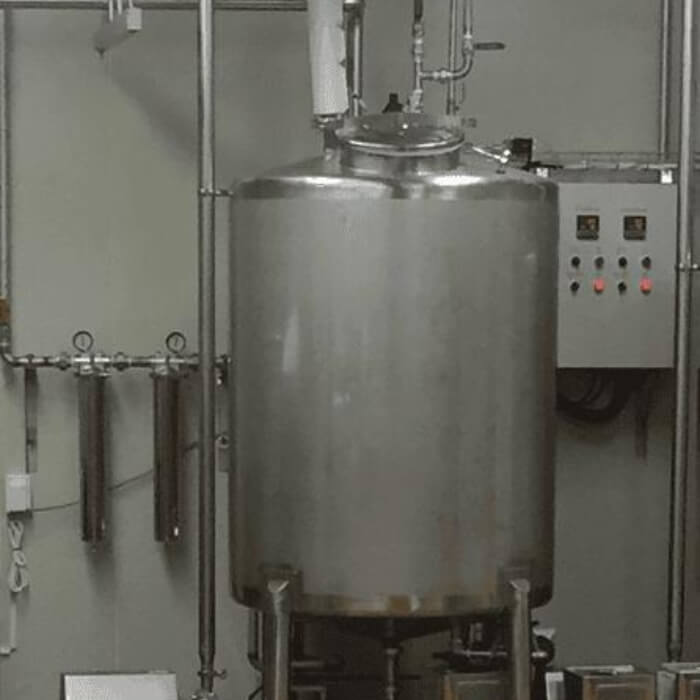

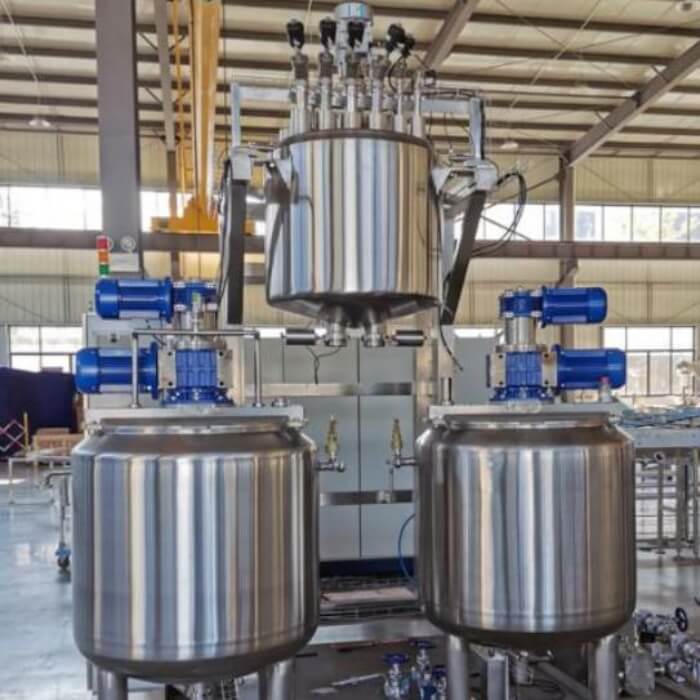
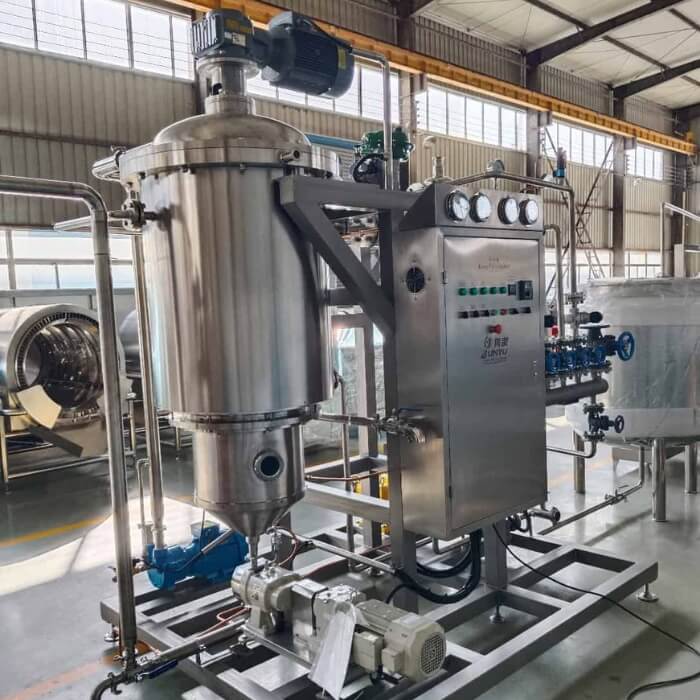
_1752819280_WNo_700d700.jpg)
2. Depositing Machine(Mogul Line)
Depositor Section designed for 1 Depositing positions and equipped with 1 pumps. Each pump deposits the entire tray by one stroke.
Following movements are driven by motors:
Tray destacking
- Small chain convey to tray overturn
- Tray overturn
- Small chain convey to mould stamping
- Mould stamping
- Chain convey to depositor
- depositor is used for making normal product
- Small chain convey to tray stacker
Tray stacking
- Tray Size: 820x400x53 Body Height (Buyer to confirm)
- Stack Height: 80pcs (40pcs X 2) per one stack
- Pallets: 3 pallets (2 stacks on one pallet) on run-in conveyor and run-out conveyor of mogul
- Maximum Speed: 22 trays per minute at 1 stroke per tray
- Normal running speed at 18-22 trays /min
- Electrical Equipment: Power 380V, 3 Phase, 50Hz/60Hz. (Buyer to confirm)
2.1 Pallet Conveyor
The empty or gummy candies with starch trays will be conveyed from the cooling room to the tray stacker and feeder frame by pallet fork lifter which moved by operator.
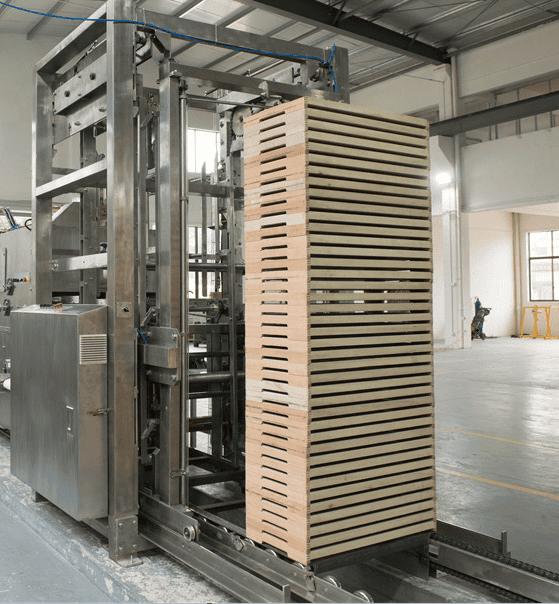
2.2 Automatic Tray Feder
The trays will be stacked (5pcs trays per stack) and lift to the tray feeder. The Feeder is equipped with input roller track on which the operator places the pallet. Standard entry method is from the end of the track. Full stack height gates are provided for positive, safe stack feeding. Full stack-height rollers ensure the stacks are straight when entering the Feeder. The gates close behind the stack and remain closed until the whole stack is safely de-stacked. The stack is first de-stacking into groups of 5 trays which are then separated into single trays. The de-stacking conveyor moves continuously.
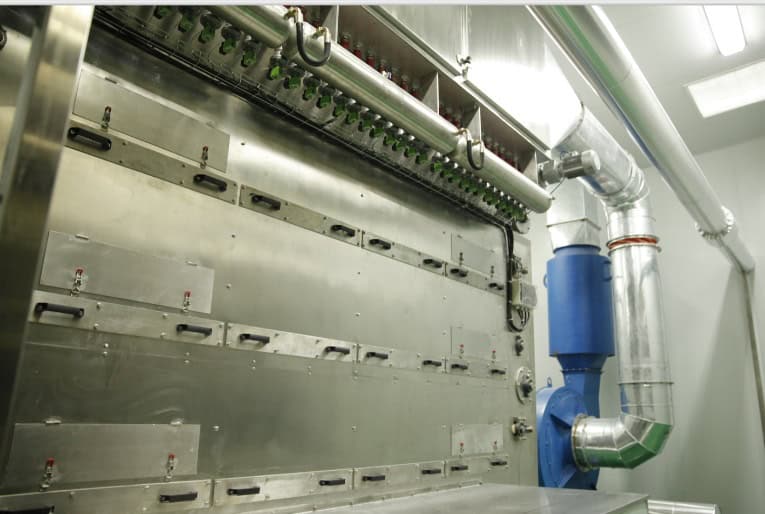
2.3 Starch Section
2.3.1 Tray emptying
With 360 degree turning table, 2 stroke working. Tray with products insert into turning table, the tray will be turn 180 degree for discharging the products into vibration sieve , then turn another 180 degree up, then be pushed out from the turn table .
2.3.2 Starch and product separation
Starch with products after discharge at turn table , will fall onto vibration sieve . with pre-starch cleaner for separate the starch and products.
With vibration sieve
With one group starch pre-cleaning system
2.3.3 Starch collection by a series of internal spirals and an external vertical spiral
After starch separate sieve, the starch will collect by the group of spiral system under the vibration sieve. Starch sent by external vertical spiral to starch conditioning system.
2.3.4 Tray filling and surface leveling.
A starch hopper positioned over the tray conveyor dispenses starch into the tray. The amount of starch is regulated by the variable speed rotary paddle in the hopper. The starch surface is smoothed by the reciprocating horizontal leveler immediately after filling.
2.3.5 Printing of product shapes in starch
It is by the complete mold board which permits pressed to be transmitted to the mold for accurate molding and clean mold lift off. A controllable pneumatic knocking mechanism is provided to free the mold cleanly and break the vacuum before the mold board is lifted. Mold board is held by quick acting lever clamps and slid into place by one man from the side of the machine. Speed of printing is adjustable according to the main speed
2.3.6 The Trays are transported through the Starch Section by one motor, it will synchronize with the main machine.
2.3.8 The Trays are transported through the Depositor Section
2.3.9 Automatic Tray Stacker.
Construction is similar to the feeder. A group of up to 5 trays is accumulated in the stacker magazine. Stacker clamps carry the groups of trays in a smooth, continuous motion and form a complete stack on the pallet at the discharge side of the section. The empty pallets are automatically delivered from the feeder to the stacker by the pallet underfeed conveyor, once the stack of tray is complete, the pallet is advanced to make room for the next stack. When two stacks are complete, the pallet is advanced further onto the roller track from which it is transported to the cooling room by small cart.
The Mogul comes equipped with electric motors, sensors and switch gear, wired to the control cabinets located on or within each section of the machine.
2.4.Starch Conditioning System
It includes drying system and cooling system. The processing of drying through vertical heat exchange principle. The starch which the humidity cannot meet the requirement of the production in the depositing machine, will be sent to starch manage machine through screw. The starch inside drying machine be suspend on the scraping board tube, the suspended starch will be sent to cooling system. This starch also will be fed by screw and cooled down by the cold air which sucks in from the heat exchanger. The finished starch will be sent to depositing machine again. The processing of starch drying will use the bag type collecting machine, and ensure collect all of the starch and no waste. No dust will flow into the room.
3. Finishing Products Section and Coating System
The finished candy will be sent inside machine and through a serial air blow mesh conveyor for separating the starch and finished candy. And the starch will be circled to starch conditioning system. The candy will be sent to oiling coating machine.
3.1 Finished Products Conveyor (Standard Length)
The finished products conveyor is especial design for the mogul plant attached with starch removing system. Continuously conveying the finished candy on this machine and simple remove the starch stick on the surface of candy, starch removing system with one couple of blowers driven by compressed air. Blower fixed on the bottom and top of the s.s conveyor belt, finish the starch removing of the candies. The top blower connecting with dust collecting pipe, this dust collect system be connected with dust collector by outer pipe.
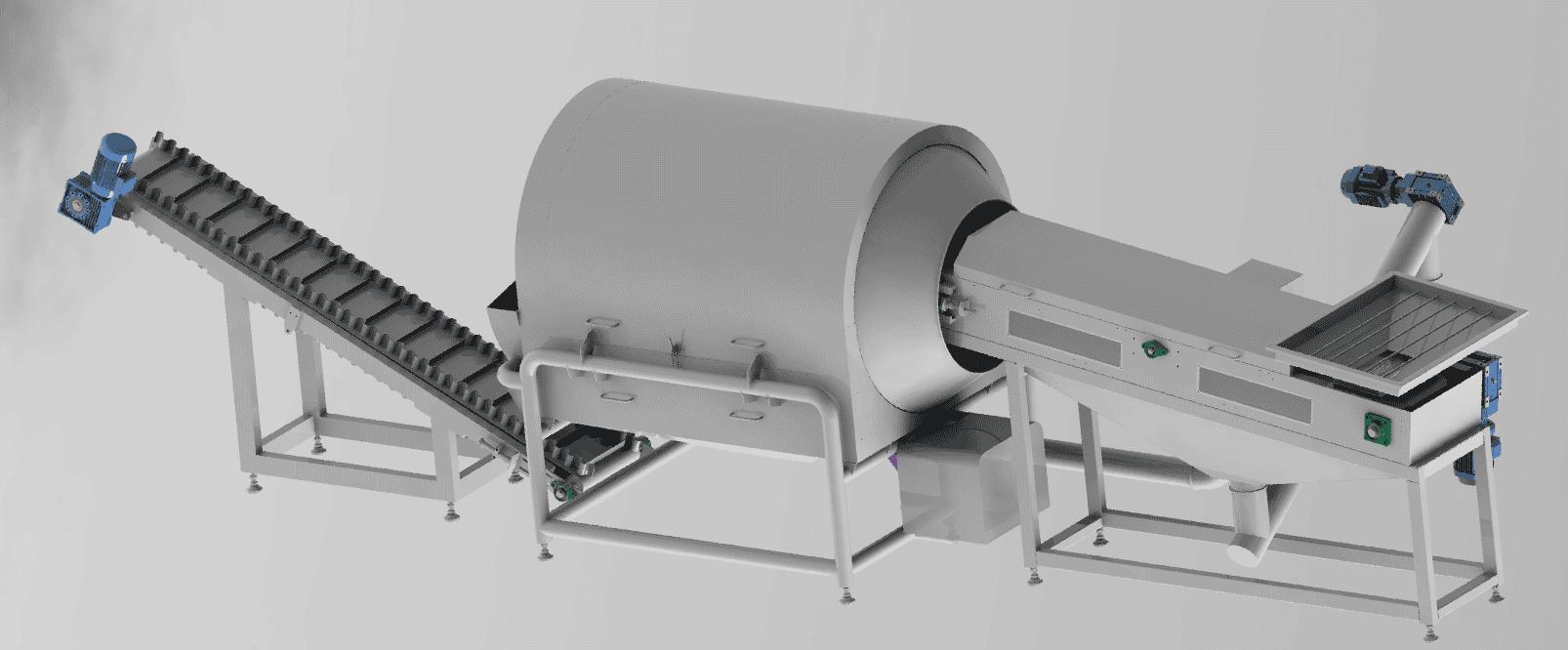
3.2 Candy Cleaner
The candy cleaner is especial design for the mogul plant. It will continuous cleaning the starch stick on the candies. Machine with 3 couple of blower driven by motor help by compressed air fix on bottom and top of the belt. Attached with dust collecting pipe, be connected with dust collector.
3.3 Suger Coating System

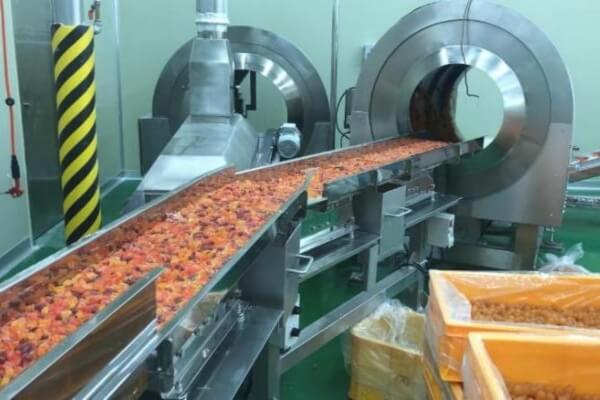
4. Curing Room/Dry Room
4.1 Description
The stack after depositing with products, then be sent into curing room for removing the moisture and parameter change of candy. Curing room is key point of processing for gummy production. The system consists on rooms, machine, piping , automatic control and so on.
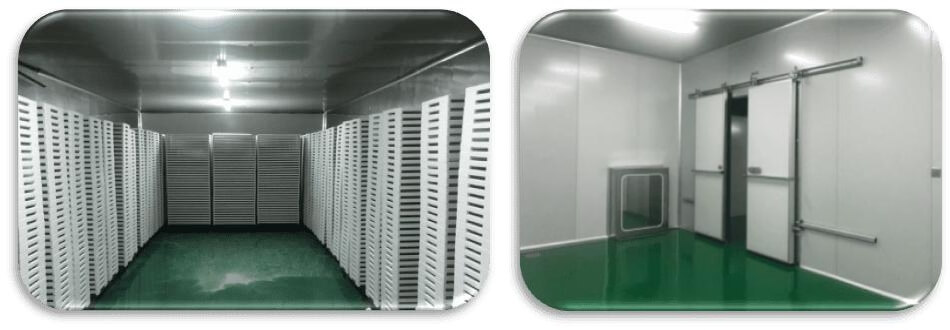
The drying room is to use the wheel dehumidifier unit and the temperature and humidity sensor to control the temperature and humidity in the studio. The products in the room are dried by cold or hot air. The cold and hot air circulation adopts horizontal air supply, and the air source is centrifugal fan.
The principle of cold drying is that the primary return air (high temperature and high humidity air source in the drying room) is cooled in the front cooling section, then the moisture in the air source is discharged through the desiccation of the runner, and then mixed with the secondary return air (high temperature and high humidity air source in the drying room), and then cooled to the set temperature and humidity in the cooling section after the cooling section. Thus, the product is kept in constant temperature and humidity state to the highest temperature and humidity The final sugar.
The principle of hot drying is that the secondary return air (high temperature and high humidity air source in the drying room) is dehumidified by evaporator in the air conditioning unit at high temperature and discharged by the exhaust fan on the air duct. The product can reach the final sugar degree by cycling.
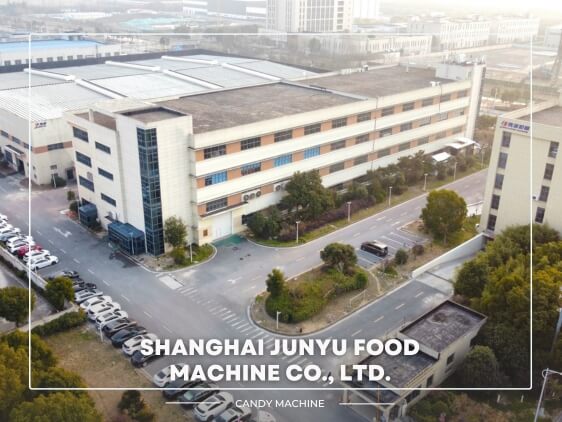
About Junyu
Top Starch Mogul Production Line Manufacturer in China
Shanghai Junyu Food Machine Co., Ltd., founded in 1987, is a leading innovator in confectionery machinery, rooted in over three decades of expertise that began with our founder’s pioneering candy machines in the early 1980s.
Based in Shanghai Fengxian Industrial Zone, we design and manufacture world-class candy production lines, delivering tailored solutions to clients in over 100 countries. We are the ideal partner for food companies, raw material suppliers and agents.
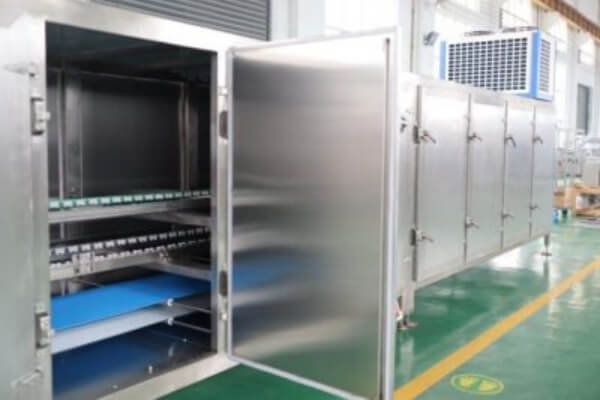
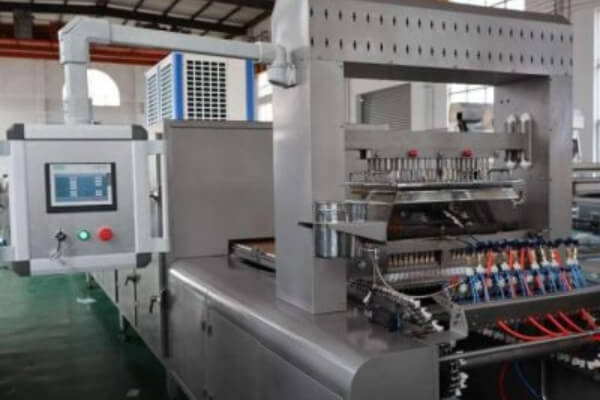
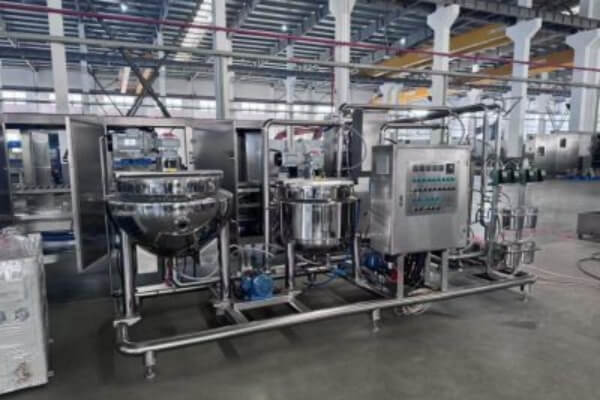
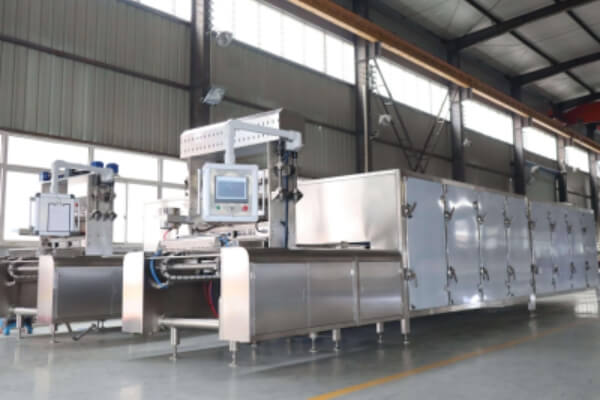
Why Choose Us
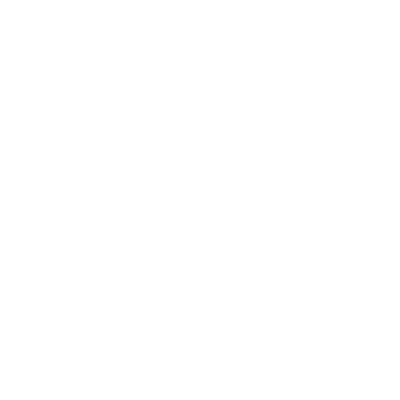
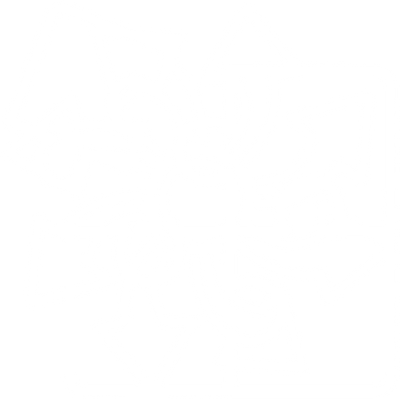
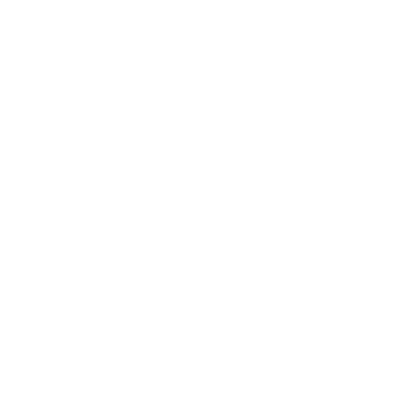
Types of Gummies We Produce
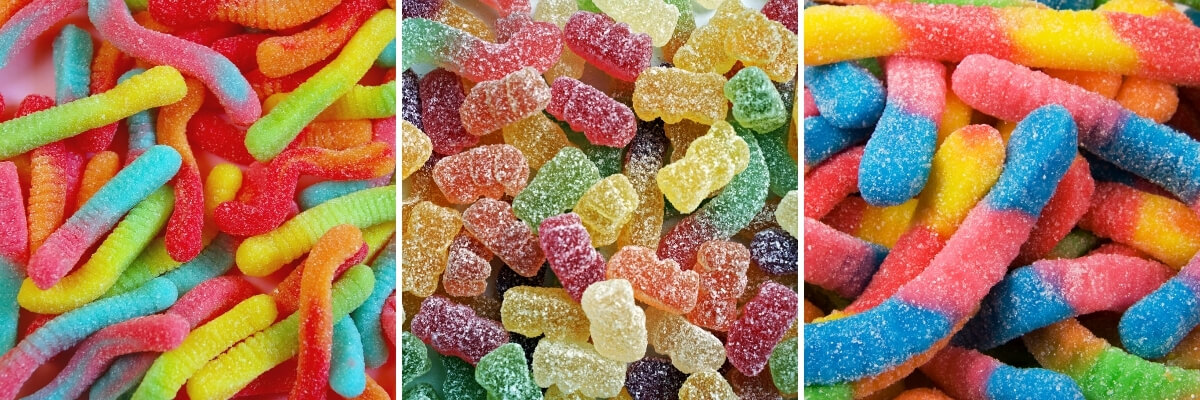